Mark Smith chatted with me yesterday and was able to steer me in some good directions and also confirmed some details with me so he can send me some more goodies. Yeah! I ran into a little different scenario as originally I had planned on using my TDI for the donor, but changed my mind later on when a local shop had a VR6 sitting in the lot collecting dust. The issue is, once you order a kit, Smyth Performance goes through their lists for parts based on the donor you're using. There are several differences between the TDI and VR6 of course, but also between 5 and 6-speed manual tranny's. So after some confirmation and good conversation, Smyth Performance will be sending me some items (like shift cable extension kit & other hardware) soon that will work for my build. I still have enough to keep me busy for a while, but it's nice to think ahead. Apparently there are 12 builds currently taking place. I don't know who they all are, but chime in anytime here if you are a beta with links and info as you see fit. BETA's I know of so far that are building now: John #1 Phillips, Clint "Redjoker" Frysinger, Bill Shaw, Bob #24 Terranova (25 min away), Uwe Lenger, Robert Zeien, Jalen Smith, and I'm pretty sure Mike Gallant's and Kim's VR6 are being worked on too at the HQ.
Not all of today was tied up in wiring. I prepped and painted the windshield frame with Duplicolor's truck bedliner spray as per Mark's recommendation. It really looks good with a little texture to it. Most of it will be covered anyway, but I wanted to seal it so the rust wouldn't be a problem. I ran short of help today, so it will have to wait for another time for a test fit. That's okay as the dash trough has the bus connectors I'm working on anyway. I only got 2 runs of cable done out of an estimated 8 or 9, so I have a long way to go, but I'm getting into a groove. Can't stress enough the necessity of good tools. I picked up a Harbor Freight ratcheting crimper, hoping it would be the stuff. Wrong. I'm having to more than double my work. Conversing with Mike tonight, he gave me a link for a pair like he uses. I'll be ordering one as soon as I start another build. This one will hopefully be done Monday or Tuesday as far as the wiring extensions go.
Underneath the car, I still had some heat shield in the tunnel to remove, disconnect the 2 O2 sensors, and remove the catalytic converter section of the exhaust. I also removed my damaged (rear right) brake line in preparation for its replacement. I spent some time untangling my mess of wiring harness, and gave Mike some feedback for his wiring section of the build manual in progress. I like Mike. He's doing some really good work. He should be in the shop tomorrow to take a look at what I have a question on. Basically I figured out all the connectors that need extension except the 2-pin connector. I have found at least 8 connectors that look like the one pictured. Some are obviously staying up front, but there are still plenty to choose from, so he's going to look and try to tell me which component or trunk line it's on. Meanwhile I will keep working on the others I know.
Friday I was able to tear apart a little more of that spare (wrecked) red VR6 that I got the motor out of. I'm not counting time on that one as part of this build unless it's directly related to something I have to do for this build. Anyway, I'm hoping to recover its brake line, K-frame, spindles, half shafts, tie rods, and a-arms for my current project. The rest of the car and parts will be sold, stored for another G3F, or taken to the scrap yard. Tomorrow I hope to get the front and rear "axle"/frame stuff off to use (I need the rear for a frame that's got no rear wheel assembly, not the G3F).
Nothing new that hasn't already been posted for pics on the wiring project, but I will snap a shot or two of the windshield and post it soon. Have fun & thanx for reading.
Intended to track progress, time involved, expenses, and other details of my first kit-car build in order to share valuable insight to encourage and help other builders to do as well or better and to entertain those who aren't building their own car. My build begins with a stock 2000 VW Jetta with a VR6 12V engine. It will emerge as a Smyth Performance G3F, oozing with awesomeness!
"Building in Style"
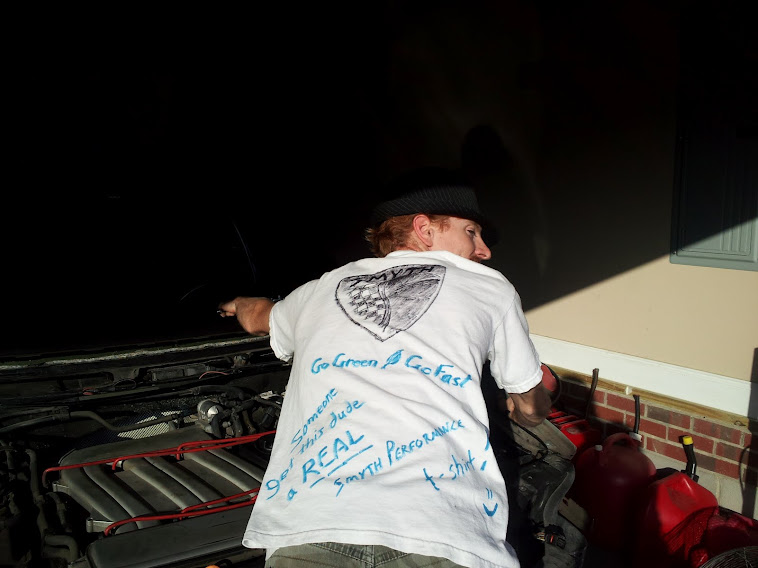
Donations for the REAL Smyth shirt are accepted lol
Saturday, August 25, 2012
Thursday, August 23, 2012
Day 15 ~ Clean up
A short night for G3F building, but not really a short night in the garage . . . I spent a good deal of time with a bucket of soapy water and a rag cleaning up all the surfaces I could see and easily get to. The engine compartment was a bit nasty, the dash trough dusty, and the rest of the car needed a good wipe-down too. A few parts still need some serious degreasing, but I'll wait until I can roll it outside and hit it with some good degreaser and hose it down.
Other than cleanup, I moved the engine mounts from front to rear and took a good look at the remaining parts I received on the pallet. Mainly the fuel cell and framework. I don't have the hardware to assemble it (nuts and bolts) unless he's reusing donor parts, but from the pictures, I don't think so. I plan to call Mr. Smith tomorrow to check on those, the shifter extension kit, and some advice on whether or not I should use VR6 front hardware (spindles, calipers, rotors) in the rear or not. From what I've seen, they're using 2.0/1.9 model front stuff as it's less beefy than the VR6 equivalent. My problem is that I have like 3 sets of VR6 spare hardware, and if we have to go with TDI, then I'm going to look into converting my TDI daily driver with a VR6 front package upgrade. That's more work than I want to get into right now, but if it's best, then that's what we're gonna do.
It seems I've spent quite a few hours planning the next few days out. I wasn't feeling too good today, and friend needs some help tomorrow getting his car back on the road, so we'll have to see if I can manage it all. Not posting goals this time, but I'll let y'all know if it all got done or not. Stay tuned, if all goes well, there's going to be a lot more pics to upload Saturday.
Other than cleanup, I moved the engine mounts from front to rear and took a good look at the remaining parts I received on the pallet. Mainly the fuel cell and framework. I don't have the hardware to assemble it (nuts and bolts) unless he's reusing donor parts, but from the pictures, I don't think so. I plan to call Mr. Smith tomorrow to check on those, the shifter extension kit, and some advice on whether or not I should use VR6 front hardware (spindles, calipers, rotors) in the rear or not. From what I've seen, they're using 2.0/1.9 model front stuff as it's less beefy than the VR6 equivalent. My problem is that I have like 3 sets of VR6 spare hardware, and if we have to go with TDI, then I'm going to look into converting my TDI daily driver with a VR6 front package upgrade. That's more work than I want to get into right now, but if it's best, then that's what we're gonna do.
It seems I've spent quite a few hours planning the next few days out. I wasn't feeling too good today, and friend needs some help tomorrow getting his car back on the road, so we'll have to see if I can manage it all. Not posting goals this time, but I'll let y'all know if it all got done or not. Stay tuned, if all goes well, there's going to be a lot more pics to upload Saturday.
Sunday, August 19, 2012
Day 14 ~ Suspension
Another weekend passes me by it seems. Actually, it has been pretty stressful for the family this week with the first week of school kicking in. My wife teaches in elementary, Jr. hi, and Sr. hi, and I help out the school on a lot of last minute details. So Saturday we took a chill day resting, playing, and doing some chores around the house. It was good to relax.
Not all was fun and games, though. I got to work separating the front spindles from the old struts, trying to leave as much as possible in tact. That can prove to be more of a pain than it may be worth, but it's not likely to be easy either way. I definitely recommend having a helper. I worked mostly alone as usual and ended up ripping the abs sensor wires on both sides as a result of not being able to hold all the various heavy pieces when things went wrong. Hangar wires are a bit flimsy for anything larger than a caliper. Oh well, it won't take long to repair later on when I work on wiring.
We reuse the upper mount hardware on the new strut, so I had to use a strut spring compressor to disassemble the old struts. Take your time to do it safely here as there's no reward for risk taken. I got a nice set of spring compressors from the local auto parts store on rental. It's good sturdy stuff made for handling the job.
I ran into a couple tough spots today though. Getting all that heavy stuff lined up just right by myself was a bear. I even got help for a few minutes, but it didn't make it any easier as we both couldn't seem to get the right angles worked out. I would recommend disconnecting at least one side from the anti-sway bar so you can work one side independently from the other. One side on the front struts slid into the spindle just fine. My biggest hold-up today was the other side that did not. Someone at the factory apparently forgot to mic the bottom of the tube at the weld. After getting it sufficiently wedged in all but the last quarter inch, and trying in vain to get it to go the rest of the way, I finally decided to take it back off and start over. Wow, I thought the old one was hard to get off. Even using a pry bar in the back to spread the clamp didn't do much good. After I gave it a good piece of my mind (and some finger-flesh too ouch) and finally got it back off, I had to use some 800 grit sandpaper to smooth out the scoring left by the strut's welds. Then I took a small flat file and worked on the welds for a while until I got them down to the cylinder diameter. QC is undeniably important. That strut should have been tossed in the "no-go" bin. Oh well. I'm still counting the time as inevitably every builder is going to face a few snags along the way.
The rear struts got hung too, but they're really just on there loosely as I wasn't able to get the tie-rod to budge. We'll be using it, but I'm going to have to replace that bolt and boot there unless I can get it to cooperate. I picked up another tool to help, but with all the trouble on the front end, ran out of time. I was hoping to have the wheels back on this weekend, but at least the front should be good for now.
Not all was fun and games, though. I got to work separating the front spindles from the old struts, trying to leave as much as possible in tact. That can prove to be more of a pain than it may be worth, but it's not likely to be easy either way. I definitely recommend having a helper. I worked mostly alone as usual and ended up ripping the abs sensor wires on both sides as a result of not being able to hold all the various heavy pieces when things went wrong. Hangar wires are a bit flimsy for anything larger than a caliper. Oh well, it won't take long to repair later on when I work on wiring.
We reuse the upper mount hardware on the new strut, so I had to use a strut spring compressor to disassemble the old struts. Take your time to do it safely here as there's no reward for risk taken. I got a nice set of spring compressors from the local auto parts store on rental. It's good sturdy stuff made for handling the job.
I ran into a couple tough spots today though. Getting all that heavy stuff lined up just right by myself was a bear. I even got help for a few minutes, but it didn't make it any easier as we both couldn't seem to get the right angles worked out. I would recommend disconnecting at least one side from the anti-sway bar so you can work one side independently from the other. One side on the front struts slid into the spindle just fine. My biggest hold-up today was the other side that did not. Someone at the factory apparently forgot to mic the bottom of the tube at the weld. After getting it sufficiently wedged in all but the last quarter inch, and trying in vain to get it to go the rest of the way, I finally decided to take it back off and start over. Wow, I thought the old one was hard to get off. Even using a pry bar in the back to spread the clamp didn't do much good. After I gave it a good piece of my mind (and some finger-flesh too ouch) and finally got it back off, I had to use some 800 grit sandpaper to smooth out the scoring left by the strut's welds. Then I took a small flat file and worked on the welds for a while until I got them down to the cylinder diameter. QC is undeniably important. That strut should have been tossed in the "no-go" bin. Oh well. I'm still counting the time as inevitably every builder is going to face a few snags along the way.
The rear struts got hung too, but they're really just on there loosely as I wasn't able to get the tie-rod to budge. We'll be using it, but I'm going to have to replace that bolt and boot there unless I can get it to cooperate. I picked up another tool to help, but with all the trouble on the front end, ran out of time. I was hoping to have the wheels back on this weekend, but at least the front should be good for now.
Tuesday, August 14, 2012
Day 13 ~ X-braces
Today was a short one after my full-time job, TDI service, dinner, and some family time at the pool. I had to grab some supplies from Lowe's and get a couple more tools for later on also. So in light of all that, I'm happy with getting the cross braces aligned, drilled, and snugly installed. Nothing much to report here other than one possible tip. The bottom bolt (M14) for the X-braces has two elongated holes provided, so leave it just barely loose enough to move around while you get the side plates flush with the frame. Then after you have the side plates tightened, go back and tighten the bottom bolt.
Also, I didn't have a 10mm drill bit handy (for the top of the x-brace), so the 3/8" had to do. That said, ya gotta give the bit a little wiggle after you punch through to widen the holes just a tad. Works good, snug, and looks good too (which is important ; ).
Goals? Yeah I like setting at least a couple goals to shoot for, so we're going to hit it again Thursday and go for getting the new shocks on...at least in the rear. It sounds simple, but it's a bugger sometimes getting the old spindles off. Note to self: remember to "rent" a coil spring compressor from O'Reilly Auto Parts tomorrow. That's all for now. Thanx for reading. = )
Also, I didn't have a 10mm drill bit handy (for the top of the x-brace), so the 3/8" had to do. That said, ya gotta give the bit a little wiggle after you punch through to widen the holes just a tad. Works good, snug, and looks good too (which is important ; ).
Goals? Yeah I like setting at least a couple goals to shoot for, so we're going to hit it again Thursday and go for getting the new shocks on...at least in the rear. It sounds simple, but it's a bugger sometimes getting the old spindles off. Note to self: remember to "rent" a coil spring compressor from O'Reilly Auto Parts tomorrow. That's all for now. Thanx for reading. = )
Monday, August 13, 2012
Day 12 ~ Post-Olympic Miscellaneous
Finally the TV is not burning constantly. It's kind of hard to buckle down working extra projects when the Olympics are on I must admit. Now that they're done for a year and a half, we're good to go.
I spent a good while today rummaging through all of the facebook albums on the Smyth Performance page, reading the various comments and seeing if I could make enough sense of the scope to press forward. It's a bit difficult for me to know what's next exactly, because some of the parts I have are installed over/on/after some of the parts I do not yet have. No matter, I still have plenty I can work on. I went through my trailer full of spare Jetta parts I've been collecting and cleaned up the extra K-member I'll be using in the rear. I was going to separate the spindles for the rear wheels, but ran into trouble on the tie-rod bolt. After fussing with it for a while I decided to move on.
The rear subframe height adjustment still had to be made, so I knocked that out as per my last post's idea. A word of caution though: if you take the rear lower mounting bracket off, make sure you don't clean it. You will need to see the original placement indicated by the dust rings. There is room for play on all four bolts, but you don't want to throw out any adjustment, so I recommend just replacing it exactly where it was when you're done with it. The subframe's lower tie-rod will likely be putting some pressure on the bracket one way or another, so keep it turned out of the way just a bit so you can remount the bracket before slipping the through-bolt in there.
On to the lower X-brace. I had to cut off a little mounting stud from the right side rail just in front of the rear mount bracket (formerly used with the fuel-line plastic retainer). Both sides have a nice little plastic plug that pops out so you can slip the 14mm bolt down through it and have room for some adjustment. Go ahead and get the nut started on that bolt with the x-brace arm. I tightened it up a little just to get it flush with the bottom surface, but loose enough to be able to still position it just right. You're going to have to drill 3 times per side, so it's handy to have the bolt hold it in place once you've got it lined up and in the center bracket. I did not end up drilling yet as it was getting too late, and I was short on hardware to put in the holes anyway. Somewhere along the way I'm out 16 washers, and one of the lock nuts I have is the wrong thread pitch, so a trip to Lowe's tomorrow should remedy that. I need to pick up a better drill bit set too, so no biggie...just frustrated my effort today to get more accomplished.
All in all, there's not a whole lot to see of the progress, but I was able to get a better understanding of some of the next steps, and I have a few more parts staged for installation. I have much higher hopes for this week than last for progress on the G3F, so stay tuned. My 240k mile services are due on my TDI (non-donor daily-driver . . . for now), so most of that will go pretty quick. I already have the oil/filter change done, and the fuel filter, air filter, and cabin air filter arrived, so they'll be going on tomorrow. The only thing that may really hold me up an extra day is the timing belt. It will be my first time, and it's not really an easy one anyway, but I gotta do it. So not worth skipping the timing belt ; )
I spent a good while today rummaging through all of the facebook albums on the Smyth Performance page, reading the various comments and seeing if I could make enough sense of the scope to press forward. It's a bit difficult for me to know what's next exactly, because some of the parts I have are installed over/on/after some of the parts I do not yet have. No matter, I still have plenty I can work on. I went through my trailer full of spare Jetta parts I've been collecting and cleaned up the extra K-member I'll be using in the rear. I was going to separate the spindles for the rear wheels, but ran into trouble on the tie-rod bolt. After fussing with it for a while I decided to move on.
The rear subframe height adjustment still had to be made, so I knocked that out as per my last post's idea. A word of caution though: if you take the rear lower mounting bracket off, make sure you don't clean it. You will need to see the original placement indicated by the dust rings. There is room for play on all four bolts, but you don't want to throw out any adjustment, so I recommend just replacing it exactly where it was when you're done with it. The subframe's lower tie-rod will likely be putting some pressure on the bracket one way or another, so keep it turned out of the way just a bit so you can remount the bracket before slipping the through-bolt in there.
On to the lower X-brace. I had to cut off a little mounting stud from the right side rail just in front of the rear mount bracket (formerly used with the fuel-line plastic retainer). Both sides have a nice little plastic plug that pops out so you can slip the 14mm bolt down through it and have room for some adjustment. Go ahead and get the nut started on that bolt with the x-brace arm. I tightened it up a little just to get it flush with the bottom surface, but loose enough to be able to still position it just right. You're going to have to drill 3 times per side, so it's handy to have the bolt hold it in place once you've got it lined up and in the center bracket. I did not end up drilling yet as it was getting too late, and I was short on hardware to put in the holes anyway. Somewhere along the way I'm out 16 washers, and one of the lock nuts I have is the wrong thread pitch, so a trip to Lowe's tomorrow should remedy that. I need to pick up a better drill bit set too, so no biggie...just frustrated my effort today to get more accomplished.
All in all, there's not a whole lot to see of the progress, but I was able to get a better understanding of some of the next steps, and I have a few more parts staged for installation. I have much higher hopes for this week than last for progress on the G3F, so stay tuned. My 240k mile services are due on my TDI (non-donor daily-driver . . . for now), so most of that will go pretty quick. I already have the oil/filter change done, and the fuel filter, air filter, and cabin air filter arrived, so they'll be going on tomorrow. The only thing that may really hold me up an extra day is the timing belt. It will be my first time, and it's not really an easy one anyway, but I gotta do it. So not worth skipping the timing belt ; )
Monday, August 6, 2012
Day 11 ~ Rear Subframe Bolt-On
Hoo-rah! Got the rear subframe bolted on tonight. It seems a bit simpler than it ended up being, but we got 'er done. Not all the holes line up necessarily, but they're pretty close. I have a couple pics that should show this and it's remedy.
The lower threaded rod support is nice to be able to adjust the subframe to the right height, but you
cannot adjust it while still attached. So I got the 4 (of 8) front B-pillar bolts in to hold it in place, then took the laser-level to check the height. You'll find the pics in Mark's facebook album that say the tow rings (at the far rear) are going to be about 3-1/2" below the laser line that's level with the lower door-sill. Once the crane was holding the subframe at the right height, I held the lower mount connector (with the through-bolt in place) up to the bottom of the threads and counted the number of threads that should be exposed when I screw it on. In my case, 14 seemed perfect on both sides. Upon putting it all back on (I took the whole thing off because I couldn't get clearance to turn the rods on but keep reading as you won't have to do that), the right side is perfect, but the left is about 1/8" low. Instead of removing the whole subframe again, I'm going to loosen (slightly) all the mounting bolts to allow natural flexing and stress equalization, unbolt the left "rear axle" through-bolt, and then remove the 4 bolts holding the stock rear axle mount to the frame. This should allow me clearance to make my 1 thread out adjustment which will hopefully raise the left rear just enough.
It's time for some sleep, so I'll make that quickie adjustment tomorrow and move on to other parts. The G3F is taking some shape with that subframe attached! I'm going to call it the G3F officially now, as it's now quite a bit less Jetta, and as of tonight a big step toward the final product.
Oh, one other note...I'm going to recommend that 2 of the 4 bolts Mark provides for the B-pillar mount be just a 1/4" longer or so. With the washers on and the thicker material at the bottom pillar mounts, the bolt didn't reach all the way through the lock-nut, effectively making it useless only holding by 3 unlocked threads. I remedied it by removing the 2 washers on either side. In order not to damage the finish on the subframe, I just stabilized the bolt with a wrench and used the socket to turn only the nut (proper procedure anyway, but critical here). There's plenty of surface area with lots of meat, so there's almost no real need for the washers, but it does look better with them.
![]() |
Don't force a bolt through that. |
![]() |
Pin a jack here... |
![]() |
Protect that finish! |
![]() |
My lower right was too far back. |
![]() |
Ratchet it at a strong point on the B-pillar. Remember you're on jack stands, so don't push or jerk! |
cannot adjust it while still attached. So I got the 4 (of 8) front B-pillar bolts in to hold it in place, then took the laser-level to check the height. You'll find the pics in Mark's facebook album that say the tow rings (at the far rear) are going to be about 3-1/2" below the laser line that's level with the lower door-sill. Once the crane was holding the subframe at the right height, I held the lower mount connector (with the through-bolt in place) up to the bottom of the threads and counted the number of threads that should be exposed when I screw it on. In my case, 14 seemed perfect on both sides. Upon putting it all back on (I took the whole thing off because I couldn't get clearance to turn the rods on but keep reading as you won't have to do that), the right side is perfect, but the left is about 1/8" low. Instead of removing the whole subframe again, I'm going to loosen (slightly) all the mounting bolts to allow natural flexing and stress equalization, unbolt the left "rear axle" through-bolt, and then remove the 4 bolts holding the stock rear axle mount to the frame. This should allow me clearance to make my 1 thread out adjustment which will hopefully raise the left rear just enough.
It's time for some sleep, so I'll make that quickie adjustment tomorrow and move on to other parts. The G3F is taking some shape with that subframe attached! I'm going to call it the G3F officially now, as it's now quite a bit less Jetta, and as of tonight a big step toward the final product.
![]() |
Bolt too short for washers. It's really fine here without them anyway (lower left B-pillar mount viewed from inside). |
Saturday, August 4, 2012
Day 10 ~ Final Cuts
Getting the last few pieces of sheet metal off according to the guidelines took a couple hours and some patience. Again, the combination of pictures an videos on the Smyth Performance blog and youtube channel proved very helpful. At least until the end of the month, when the build manual is expected to be final drafted, I recommend spending a good amount of time perusing these. Still, there's a little bit of questions that can come up even when your staring at your car and the pictures. A final review of the pertinent videos and a couple texts to Mark showing a picture of my question and getting some advice got me going.
At long last, I'm ready to start the rebuilding segment! I'll have to read up on the blog and look at the next album of pics on facebook, but I plan on starting this maybe Monday. Today was a short day on the build, but with a constancy of life/work, I need a little break. Going to go enjoy some worship tomorrow at my church, and probably crash the afternoon at a friend's place. More pics to come soon . . . and progress too!
Another FYI for you betas in waiting. If you're not using your donor constantly, go ahead and start gutting and cutting. I've got quite a bit of time invested already without ever having to touch the kit parts yet. You can be confident that there's plenty to do to get ahead if you have the time and space.
At long last, I'm ready to start the rebuilding segment! I'll have to read up on the blog and look at the next album of pics on facebook, but I plan on starting this maybe Monday. Today was a short day on the build, but with a constancy of life/work, I need a little break. Going to go enjoy some worship tomorrow at my church, and probably crash the afternoon at a friend's place. More pics to come soon . . . and progress too!
Another FYI for you betas in waiting. If you're not using your donor constantly, go ahead and start gutting and cutting. I've got quite a bit of time invested already without ever having to touch the kit parts yet. You can be confident that there's plenty to do to get ahead if you have the time and space.
Friday, August 3, 2012
Day 9 ~ Last Prep. for Final Cuts
As usual, things took a little longer than I expected, but we're good to go on the cutting tomorrow. I got the rest of the harness out of the way along the left inner fender support area, the windshield trough, and the dash area. I also cleaned out the wiper motor and assembly, computer, and cabin air intake from that windshield trough area just to make sure I don't mess anything up when the blades go flying in there soon.
The dash took me a while to lower out of the way too. Just like engines the first time around, there always ends up being something else holding it up. A few connectors and harness straps needed to be removed, but the stupid part about the thing that I couldn't see for some reason was that 3-bolt dash support that bolts to the left inside A-pillar. I suppose I could have read that in the Bentley manual, but then I'd have wasted a bunch of time reading all the other steps that had already been done before I got the manuals. Something in Mark's pictures on the facebook cutting album and his blog reminded me of this piece, and sure enough once that was gone I could gently lower the dash enough to get out of my way for the cuts.
As I'm sitting here typing I just remembered a part of the inner dash cut that I didn't mark, but other than that I'm ready to hack up the front end and most of the rear. There's still a question for me on the rear final cut, but I'll have to call Mark tomorrow on that.
NOTE: I knew I'd watched some of these before, but as they didn't make much sense to me without the thing in front of me, I'd long forgotten they existed until today. Thanks to JLP's build blog that I've read through several times, I noticed the link to Mark Smith's video's on YouTube. These provided great clarity and confidence now that I've actually gotten there. I will also post links in my sidebar for this purpose. Had I watched these last week, I could be a bit farther along. Not too far though, as usually I find plenty to do to keep going.
Well tomorrow I'm off to start my day tracking down a reciprocating saw I can borrow as my own hasn't turned up. Due to the regular knowledge of inventory and location of all my tools, I'm beginning to believe my wife who thinks I didn't actually buy one, just shopped for it. Well, if my neighbor doesn't have one, I'm off to Fayetteville to go get one. It's okay really as I'll probably need a couple more blades anyway. Just bummed I didn't remember them right after work today. I guess that's the banes of living way out of the big cities. Maybe I'll get a good bike ride in. Been really missing that lately. = )
Thursday, August 2, 2012
Day 8 ~ Engine Removal [part 2]
Another long day at work with only a couple hours to "play" at the end . . . and the engine is out! Wow, those half shafts took a while for me to get all the bolts out with that M10 triple square bit. That and I had to mess around with the jack stands a bit. I tried to jack the car up from the K-member but with all the weight gone in the rear, it kept wanting to tip over on the nose. Time to call for some help from my lovely assistant. "Sit on the back for me, Babe, while I get this car all situated." Sometimes just having some company makes it all seem more fun, and sometimes it's just plain not safe without a helper. I'm not counting the half hour it took us to figure out where the heck to put the motor/tranny combo as I don't have any room in the garage to even get it around the Jetta to the rear. So, we decided to hoist it while still on the cherry-picker up into the bed of my Dakota. Then I had to find the right angle to rest it so as not to bend or break anything that I'll still be needing. I strapped it down good and will take it down to the shop to swap the motors and work on refurbishing the setup there sometime in the future.
Meanwhile, I have still a bit of piping and hardware to remove, but I'm exhausted, and need to read up on some earlier beta's notes to make sure I don't waste any time removing something that may stay. Regardless, I got an email off to Mark, and he's gonna get with me to clarify any questions so I can prepare for the final cuts tomorrow. I'm leaving the whole evening for the unexpected "that's still in my way doggone it!" pieces, but I'm still planning to have all my final cuts done Saturday.
Can't wait to get some parts back on the car! But I'm not going to rush-job it. I'll make sure things are clean and tidy a bit, so I don't have a mess underneath when I'm all done. But that's the way I am . . . try to do it right the first time even when it takes extra time up front (up to a balance point, no one's looking to waste time here). It will be worth it later. I'll get some more pics taken and uploaded tomorrow so I can edit this post and bring in a little flavor.
= )
Meanwhile, I have still a bit of piping and hardware to remove, but I'm exhausted, and need to read up on some earlier beta's notes to make sure I don't waste any time removing something that may stay. Regardless, I got an email off to Mark, and he's gonna get with me to clarify any questions so I can prepare for the final cuts tomorrow. I'm leaving the whole evening for the unexpected "that's still in my way doggone it!" pieces, but I'm still planning to have all my final cuts done Saturday.
Can't wait to get some parts back on the car! But I'm not going to rush-job it. I'll make sure things are clean and tidy a bit, so I don't have a mess underneath when I'm all done. But that's the way I am . . . try to do it right the first time even when it takes extra time up front (up to a balance point, no one's looking to waste time here). It will be worth it later. I'll get some more pics taken and uploaded tomorrow so I can edit this post and bring in a little flavor.
= )
Wednesday, August 1, 2012
Day 7 ~ Engine Removal [part 1]
Hoses, belt, connectors, etc. My goodness there's a bunch to disconnect to be able to pull the engine w/o damage. I "only" got the ignition wiring, serpentine belt, belt tensioner assembly, radiator(s), condenser coil (had the r134 recovered already), power steering pump, air conditioning compressor, alternator, water hoses, fuel & evap lines, vacuum hoses, battery & tray, air box, intake manifold, and electrical wiring harness disconnected and out of the way. Other than that, I removed a few brackets and do dads here and there.
Labeling is key! I used masking tape and a marker to label most of my wiring connectors and hoses (I say most, but recommend all especially if you're unfamiliar yet as to what does what in the engine compartment). I didn't personally choose to label everything because I've removed a handful of engines now and have a basic system that works for me. Oh, if you don't know what every little component is and what it goes to that's fine! Sometimes the thing that works is using numbers to label both sides of a connection. If you start from say a large portion of the harness near the battery, you just label the first connector "1" with a piece of tape around the wire (again, on both sides of the connection). Follow the strand as it gets smaller out to the ends, then come back to where it really branched off and continue down each branch progressively increasing your numbers. This helped me dramatically the first couple times I pulled an engine. No looking around wondering if you got them all...just keep counting up when you put them together. For the odd exception, it's helpful to have a sheet of lined paper handy to jot the numbers down so you can check them off if you feel the need to put them back together out of order. You don't want to turn the key and have some stuff disconnected. It's much more difficult to figure out what's wrong once everything's back together than it would be to follow a sequence. Also the lined paper is helpful to educate yourself as you figure out the names of the components. Just jot it down beside the number and you'll be sharp as a tack in no time.
Most people are recommending the "Bentley" manual to follow for a good disassembly order. I would agree. I got the Haynes, and compared to the Bentley, it's a different world. Informative, clarity, comprehensive...these are all words which don't apply to the likes of Chilton and Haynes but do fit the Bentley. It cost me about $80 to get a new hardback 2-volume set, but it's worth it. Even so, there are a couple errors (to be expected with almost any technical manuscript I've seen), but even when it wasn't clear, it still proved a good guide anyway. Besides, if something's in your way and hard to get to, just remove it. We're gutting the thing and moving it all back to the rear anyway, so no need for acrobatics and special tooling. Just keep track of where you are in the process so you can refer back to it when you're done with your rabbit trail.
Well, there's still the 6 exhaust manifold bolts, 3 engine mounts, and half-shafts to remove, plus the one or two wires I inevitably missed on the first pass. Then we'll be in business pulling the engine/tranny combo. I'll be separating the tranny to swap engines with another VR6 Jetta's I just picked up a couple days ago and pulled. The separation and mating of the motor and tranny will not be counted in the build time unless it becomes apparent that it needs to be done for the average builder. In my particular case, I have a bad motor that needs serious work, which I'll swap with one that will hopefully only need a little tlc.
No pics today...too tired and there's nothing much exciting about engine removal prep.
Goals:
Thursday ~ Finish engine removal and gut the remaining things that need removal along the wheel wells and firewall/dash area.
Friday ~ Get a better understanding from Mark about the final rear-cut lines (I marked them up, but something doesn't look the same as his pictures, so I'd better check first) by Friday so I can finish the remaining cuts
Saturday ~ Rust-prevention-paint-spray all the cut areas, & start putting kit parts on the Jetta!
We'll see if I'm overzealous or not. I'm getting pretty tired out with late nights and long, hard, hot days at work. The body's really starting to complain. I'm hoping to work through it and just get used to it after a while like I've done before. If not, I'll have to just rest a couple days. I really want to get all the kit parts I have installed. Then if more haven't arrived by then, I can take a break, work on the motor, or gut and scrap the wrecked VR6 frame I just got the other day for the motor. I'll be scavenging anything useful. Then it's off to the metal recycling yard for some cash. = )
Labeling is key! I used masking tape and a marker to label most of my wiring connectors and hoses (I say most, but recommend all especially if you're unfamiliar yet as to what does what in the engine compartment). I didn't personally choose to label everything because I've removed a handful of engines now and have a basic system that works for me. Oh, if you don't know what every little component is and what it goes to that's fine! Sometimes the thing that works is using numbers to label both sides of a connection. If you start from say a large portion of the harness near the battery, you just label the first connector "1" with a piece of tape around the wire (again, on both sides of the connection). Follow the strand as it gets smaller out to the ends, then come back to where it really branched off and continue down each branch progressively increasing your numbers. This helped me dramatically the first couple times I pulled an engine. No looking around wondering if you got them all...just keep counting up when you put them together. For the odd exception, it's helpful to have a sheet of lined paper handy to jot the numbers down so you can check them off if you feel the need to put them back together out of order. You don't want to turn the key and have some stuff disconnected. It's much more difficult to figure out what's wrong once everything's back together than it would be to follow a sequence. Also the lined paper is helpful to educate yourself as you figure out the names of the components. Just jot it down beside the number and you'll be sharp as a tack in no time.
Most people are recommending the "Bentley" manual to follow for a good disassembly order. I would agree. I got the Haynes, and compared to the Bentley, it's a different world. Informative, clarity, comprehensive...these are all words which don't apply to the likes of Chilton and Haynes but do fit the Bentley. It cost me about $80 to get a new hardback 2-volume set, but it's worth it. Even so, there are a couple errors (to be expected with almost any technical manuscript I've seen), but even when it wasn't clear, it still proved a good guide anyway. Besides, if something's in your way and hard to get to, just remove it. We're gutting the thing and moving it all back to the rear anyway, so no need for acrobatics and special tooling. Just keep track of where you are in the process so you can refer back to it when you're done with your rabbit trail.
Well, there's still the 6 exhaust manifold bolts, 3 engine mounts, and half-shafts to remove, plus the one or two wires I inevitably missed on the first pass. Then we'll be in business pulling the engine/tranny combo. I'll be separating the tranny to swap engines with another VR6 Jetta's I just picked up a couple days ago and pulled. The separation and mating of the motor and tranny will not be counted in the build time unless it becomes apparent that it needs to be done for the average builder. In my particular case, I have a bad motor that needs serious work, which I'll swap with one that will hopefully only need a little tlc.
No pics today...too tired and there's nothing much exciting about engine removal prep.
Goals:
Thursday ~ Finish engine removal and gut the remaining things that need removal along the wheel wells and firewall/dash area.
Friday ~ Get a better understanding from Mark about the final rear-cut lines (I marked them up, but something doesn't look the same as his pictures, so I'd better check first) by Friday so I can finish the remaining cuts
Saturday ~ Rust-prevention-paint-spray all the cut areas, & start putting kit parts on the Jetta!
We'll see if I'm overzealous or not. I'm getting pretty tired out with late nights and long, hard, hot days at work. The body's really starting to complain. I'm hoping to work through it and just get used to it after a while like I've done before. If not, I'll have to just rest a couple days. I really want to get all the kit parts I have installed. Then if more haven't arrived by then, I can take a break, work on the motor, or gut and scrap the wrecked VR6 frame I just got the other day for the motor. I'll be scavenging anything useful. Then it's off to the metal recycling yard for some cash. = )
Subscribe to:
Posts (Atom)